“ 随着现代工业的发展和需求的不断提升,精密加工已呈现专业化发展方向,对零部件精度要求和机构设计的微型化需求越来越高。DeburringTec去毛刺&表面精加工展专注于如何实现“高速·高效·精密·微细·自动化·绿色化”的现代精密加工技术体系,推出系列前沿创新的技术、工艺、设备和应用,为工业零部件去毛刺、表面精加工与精密清洗等表面处理提供高效和可持续的技术与案例参考。
”技术案例
新能源汽车精密零件的完美塑形大师
由特斯拉、比亚迪和其他各种电动汽车 (EV) 等开拓者发起的电动汽车革命已经获得了不可阻挡的势头。同时,随着消费者对电动汽车的需求持续上升,原始设备制造商和供应商将需要更积极地转向设计合理的生产线。
电动汽车总体趋势将是金属零件数量大大减少,但在加工汽车零件时,对更高质量表面光洁度和公差的要求会随着零件复杂性的增加而增加。为汽车行业的原始设备制造商供货的企业需要使其客户群多样化,并寻求其他行业以确保产能不会出现灾难性损失。新能源汽车动力电池、底盘、外壳、触摸屏、电机、马达均涉及精密加工,新能源汽车生产线的建设催生大量对精密加工中心的需求。
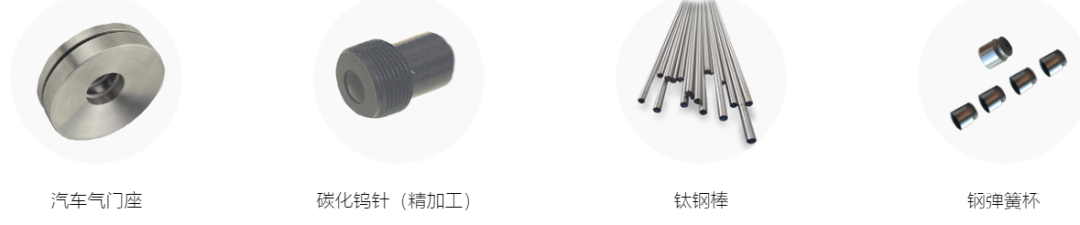
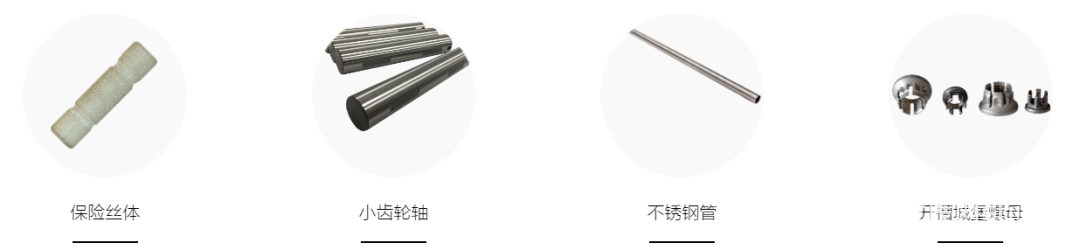
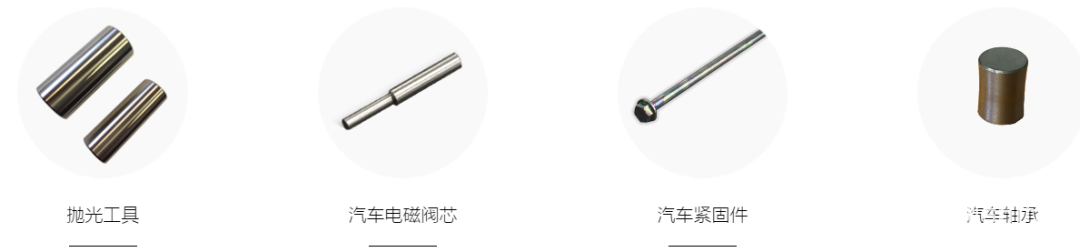
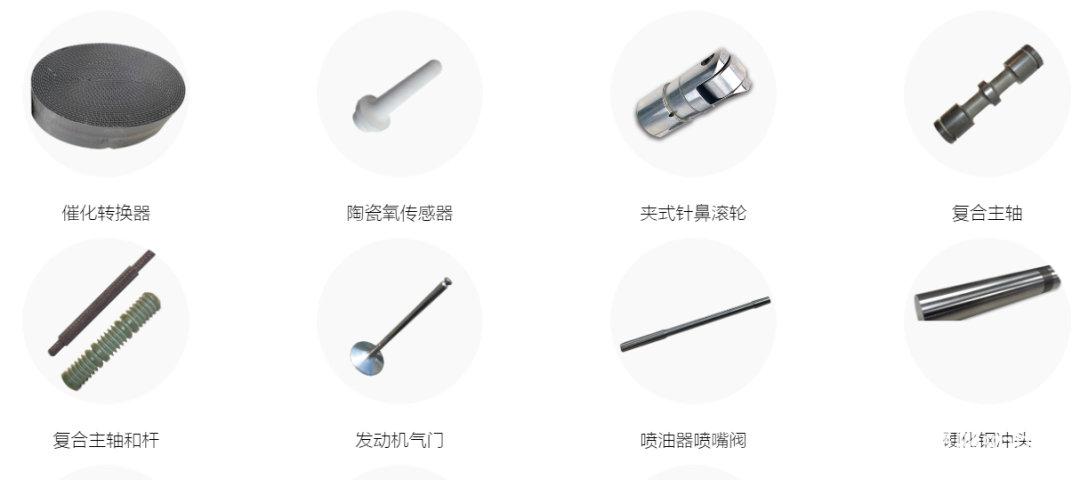
图源:glebar
# 电动车加工要求
驾乘体验以及市场追利需求破事原始设备制造商及其供应商正在改变制造的组件以及它们的制造方式。我们列出了电动汽车行业对加工汽车零件的一些要求如下。
电池制造——电池制造将成为未来电动汽车生产的瓶颈。特斯拉预见到了这一点,并计划通过建造称为超级工厂的电池制造中心来减轻这种影响。汽车公司将需要涉足电池生产,因为市场已经因全球电动汽车采用有限而变得紧张。比亚迪还承担了电池组的制造。电池生产并非易事,需要精密加工,只有先进的数控铣床、车床和磨床才能实现。
动力总成制造——电动汽车的动力总成远没有典型的内燃机动力总成复杂。原始设备制造商及其供应商将能够过渡到制造这些传动系统,而对其现有机器和工艺的改动很小,尽管产量较小。
车身面板——这些面板是通过将金属板冲压或拉制成所需形状的模具来制造的,以制造现代乘用车的复杂形式。用于此过程的模具是使用 5 轴机器加工的。一旦制造过渡到电动汽车,这个过程就不会改变。
更高的质量——由于电动汽车的相对简单性和由此产生的低维护要求,重点将转向生产更高质量的零件。为了使机加工零件的使用寿命与电动汽车的电子部件一样长,它们需要使用能够满足所需精度和可重复性的机械制造。
轻量化——电动汽车对超重非常敏感,因此零件需要由轻质航空航天材料制造。还将使用生成设计和拓扑优化等优化技术设计零件。由于这些算法会产生复杂的有机形状,因此这些复杂的零件将比传统的汽车零件需要更多的时间来制造。
低噪音——电动汽车在设计上很安静。但是,如果加工不良的零件产生过大的噪音,则浸没会中断。获得降低噪音所需的表面光洁度的最简单方法之一是使用可以达到所需公差的专用磨床。
那么有没有满足上述所有要求的精密加工方法?答案是有,精密磨削便是最具代表性的技术路线之一。
图源:3M
# 精密磨削的概念及技术标准
精密磨削(Precision Grinding)是一种注重精度的磨削形式。在金属零件具有紧密公差的地方,它被用来获得高表面质量的光洁度。它能够完全精确地磨削小尺寸,比如小到0.25到0.50毫米的深度。这种精度在误差范围很小以及需要更好精加工材料的加工领域。例如:
精密磨削多才多艺,能够处理各种材料,并遵循其规格制造优质部件,例如:

图源:edmdept
精密磨削制造过程使用由磨粒组成的专业旋转砂轮,从正在加工的工件上去除材料。砂轮是一种消耗性砂轮,用于各种磨削和磨料加工操作。由陶瓷、金属或塑料材料制成的零件非常适合这种工艺,该工艺通过在每次通过砂轮时去除非常薄的材料层来产生极其光滑和平坦的表面。
精密磨床围绕着一个装有砂轮的电动主轴建造。在它下面是一个工件夹持装置,通常是一个磁吸盘。卡盘在工件加工时将工件固定在静止位置。然后磨料砂轮在工件表面上通过,同时随着每次通过而越来越靠近工件降低。每次通过时对材料切割量的这种极其可控的调整可以实现严格的公差。它可以产生非常精细的饰面和非常精确的尺寸;然而,在大规模生产环境中,它也可以非常快速地粗加工大量金属。
在先进的加工中心,精密磨削的能力标准从直径 0.1 毫米到 300 毫米开始,长度从 2 毫米到 1200 毫米,公差低至 ±0.001 毫米(+/- 0.00005 英寸),微光洁度低至 0.6ra,主要指标如下:
外径公差小至 +/- 0.00005" (±0.001mm)
内径公差小至 +/- 0.00005" (±0.001mm)
圆度为 +/- 0.00005" (±0.001mm)
圆柱度为 +/- 0.00005" (±0.001mm)
磨削表面光洁度0.6Ra~0.8Ra
直径从 0.1mm 到 300mm
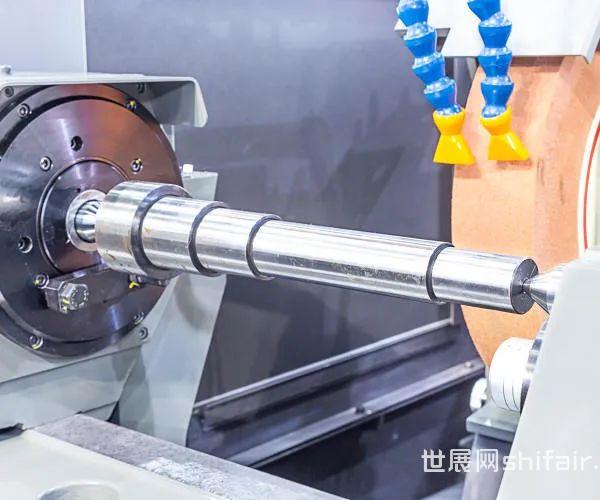
图源:dekmake
# 精密磨削的类型
选择使用以下哪种磨削操作取决于尺寸、形状、特征和所需的生产率。精密磨削类型分为平面磨削、无心磨削、内圆磨削、外圆磨削及其形式的技术手段。
平面磨削:(Surface Grinding)使用旋转砂轮磨平金属或非金属材料的平面,使其外观更精致或达到功能目的所需的表面。可以将材料的外层重新塑造和修整为理想的光滑和平坦表面。在这里,磨料砂轮位于顶部,当工件被固定在卡盘上时它会旋转。
无心磨削(Centerless Grinding):无心磨削用于加工没有固定零件或中心的地方。它适用于棒材和管材的外径。顾名思义,它无需将工件固定在某个位置即可工作。相反,无心磨床在固定位置通过控制轮和砂轮移动。这允许它在非常长的棒材和管材上工作。
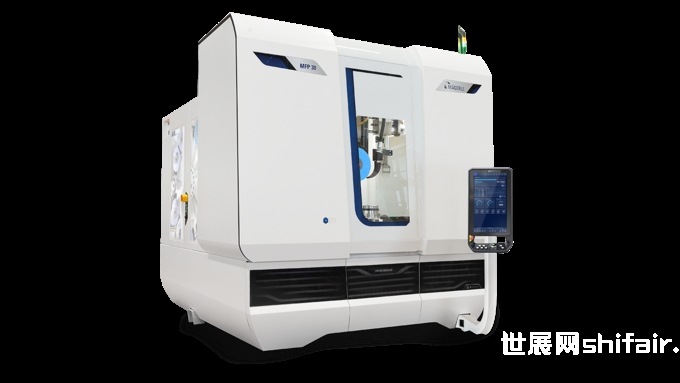
精密磨削机床 图源:UNITED GRINDING
内圆磨削(Internal Grinding):或内径(ID)磨削用于磨削零件孔的内径。它使用微型高速砂轮加工管状或管状零件。应用的高速有助于保持适当的表面速度。卡盘或夹头在操作过程中将工件固定到位。
外圆磨削(External Grinding):也称为中心型磨削,使用外圆磨床将工件表面修整或重新调整成圆形。工件放置在机器的中点,同时驱动爪、驱动爪或中心驱动器旋转工件。不同的电机以不同的速度旋转砂轮和工件。
超硬磨削(Superabrasive Grinding)该技术使用由硼砂、金刚石和立方氮化硼 (CBN) 等硬质材料制成的磨床。超级磨料机可以代替两种或多种标准方法工作。这是因为它允许更精密的加工公差并减少刀具磨损。
螺纹磨削(Thread Grinding):这种金属去除过程是通过单点形成的轮子或接触来完成的。它通常用于加工丝杠、蜗杆和滚珠丝杠。
夹具磨削(Jig Grinding):夹具磨削与圆柱和表面精密磨削有很大不同。这是因为它可以生产形状和质量更复杂的工件。夹具磨削的显着特征之一是铣床。
蠕动进给磨削(Creep Feed Grinding)):该过程涉及使用独特或复杂的研磨设备。缓进给砂轮以较长的速度工作,以避免错误并提高精度。它在自然难以研磨的材料中产生复杂的形状或槽。这些材料包括高温镍基航空合金和预硬化工具金属。
单盘和双盘磨削(Single and Double-Disc Grinding):这种类型的精密磨削使用一个大砂轮来为许多生产制造平坦、平行的工件。双盘磨床是带有两个不相连的砂轮的机器。零件在运行过程中通过这两个独立砂轮的表面。
# 精密磨削的好处
现代工业设备、零部件、组件表面越来越精微、构造越来越严格,部件表面和内部尺寸需要精密磨削来制造。虽然有其他替代方法和技术,但精度上需要有所保证的,因此精密磨是一种更具成本效益的生产方法。
除了成本效益和精度之外,采用精密磨削还有许多其他好处:生产率的提高和易于监控意味着在高效生产过程的同时,质量控制可以得到持续的保持。除此之外,它还提供非常精细的表面光洁度和高质量的最终产品。
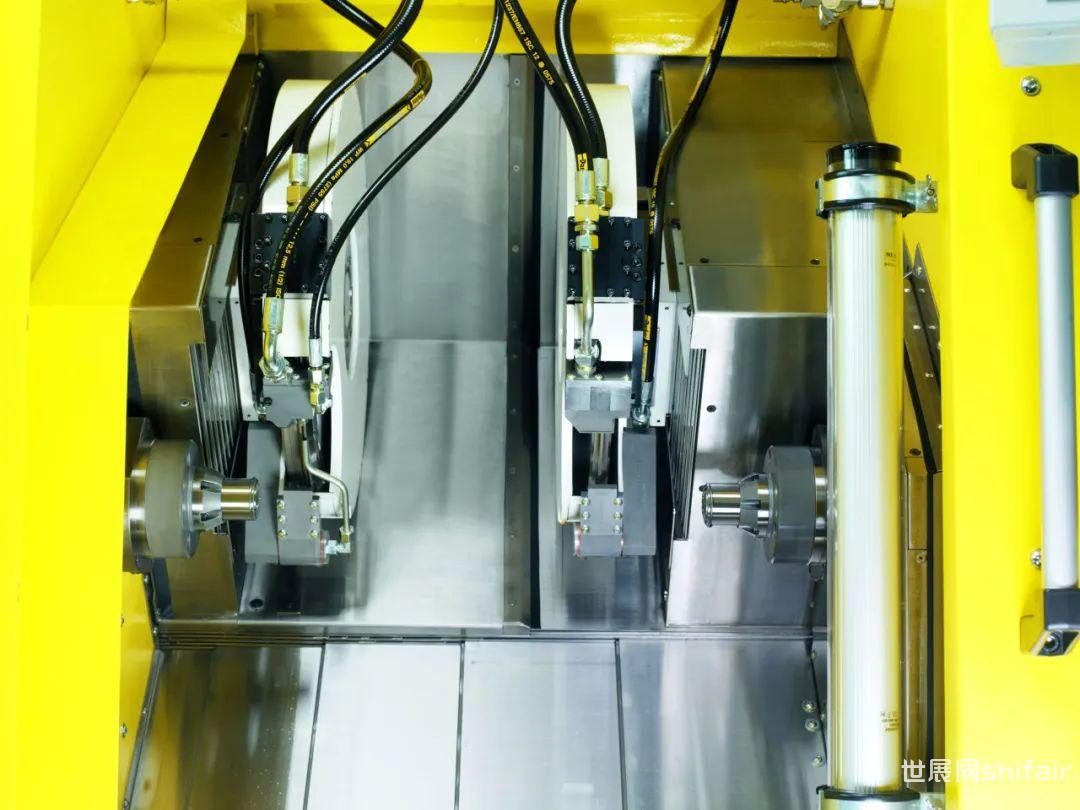
图源:productionmachining
# 电动汽车零件的塑形大师
在快节奏、充满活力的新能源汽车行业中,您需要一台能够满足不断变化的需求的精密磨削磨床。
汽车工业需要大批量的零件,所以供应商必须找到最经济的方法来生产尽可能多的零件。新能源汽车由成千上万个零部件组成,依靠复杂的设计和精密零件来尽可能可靠和安全地运行。CNC 磨削服务可满足几乎所有汽车部件的独特设计和严格的公差要求。
精密磨削技术及其磨床在设计时考虑到了灵活性,以处理各种不同的几何形状和轮廓,以及各种轴尺寸。通过精密磨削代替车削生产零件,可以生产完整的零件,从切割到仿形,提高过程可靠性,最大限度地减少机器停机时间,并消除二次操作,如表面研磨和抛光。与车削零件相比,精密磨削加工的零件具有更高的尺寸精度和更好的表面质量。该工艺也不会在零件上产生毛刺或切屑痕迹。砂轮具有冷却系统,可确保砂轮连续工作六个月或达到300,000个零件的产量。
这对于电动汽车行业尤其重要,在电动汽车行业中,一辆汽车内可能有多种轴尺寸/设计。精密磨削是自动化解决方案,可以处理电动汽车的电池组件、紧固件、弹簧杯、阀座、挺杆、摇杆销、螺线管等高精度部件。
# 案例:凸轮轴/ 曲轴 无心磨削
无心磨削主要用于制造汽车零件和发动机,以及凸轮轴、曲轴、滚针、输入轴和喷油器柱塞等部件。这种部件要求精密和高标准的紧公差,以便在它们的每个指定应用中完美地发挥作用。通过在研磨操作过程中去除研磨材料,可以获得精确的抛光和光洁度。也就是说,无心磨削不需要主轴或夹具来支撑被磨削的工件。这只是关于砂轮、调节轮和工作刀片的定位问题。
无心磨削 图源:advancegrinding
无心磨削已广泛用于实现定制尺寸。为了达到不同的尺寸、形状和光洁度要求,无心磨削分为两种主要形式:
贯穿进给/贯穿进给磨削:如果要磨削长而圆的棒料,直通磨削是最有效的。这一过程是通过将工件送入机器来完成的,工件在机器中被调节轮牵引,并从对面送出。直通进给(通常称为“直通进给”)方法非常高效,因为不需要单独的进给机构,尽管这些方法只适用于简单圆柱形的工件,如活塞、管、活塞销和棒。
进给/切入磨削:如果需要将相对复杂的零件和形状磨削到非常精确的光洁度,进给/切入磨削是最适合的。齿轮轴、曲轴、凸轮轴和其他高度复杂的汽车部件需要进行进给磨削,以达到所需的磨削和光洁度。在这种情况下,工件被装入机器,允许调节轮移动到位。零件形状的复杂性要求精确磨削,以防止工件轴向进给通过机器。
# 案例:加工液压齿轮泵齿轮轴/液压控制阀-提升阀 外圆磨削
对于加工加工液压齿轮泵齿轮轴/液压控制阀-提升阀,外圆磨削和外圆磨床已被成熟地开发用于这些高精度工件磨削。以外圆磨床为例,当采用天然花岗岩床身和运动轴直线电机驱动,具有极好的精度和热稳定性,用于有着最高要求的领域。也适用于磨削非圆工件。用水冷电主轴,兼顾常规磨削和高速磨削。最大线速度140m/s,能够在保持最大扭矩条件下进行常规磨削(60m/s)和高速磨削(140m/s)。 直驱B轴和多砂轮应用实现多功能性和高柔性。通过集成定制化自动上下料系统,满足全自动生产,保证上下料时间最短(2~6s)。
# 案例:电机高速转轴 纵向磨削法/切入磨削法电动汽车磨削技术提出了新的挑战。到目前为止在内燃机中常见的转速(大约2,500~8,000转/分)在电力驱动中增加了5~20倍。在最坏的情况下,非最佳磨削齿轮会导致机油泄漏、润滑剂泄漏和发动机损坏。因此必须确保高速电机的转轴精加工。与其他零部件相比,电机的转轴的机加工工序相对多一些,要经过粗车、精车、磨削和铣削等工序,其中磨削的部位包括轴承位、轴伸位和绕线转子电机集电环位等。电机的轴伸有圆柱形,也有圆锥形;特别是对于圆锥形轴伸,是体现磨削技术的关键。
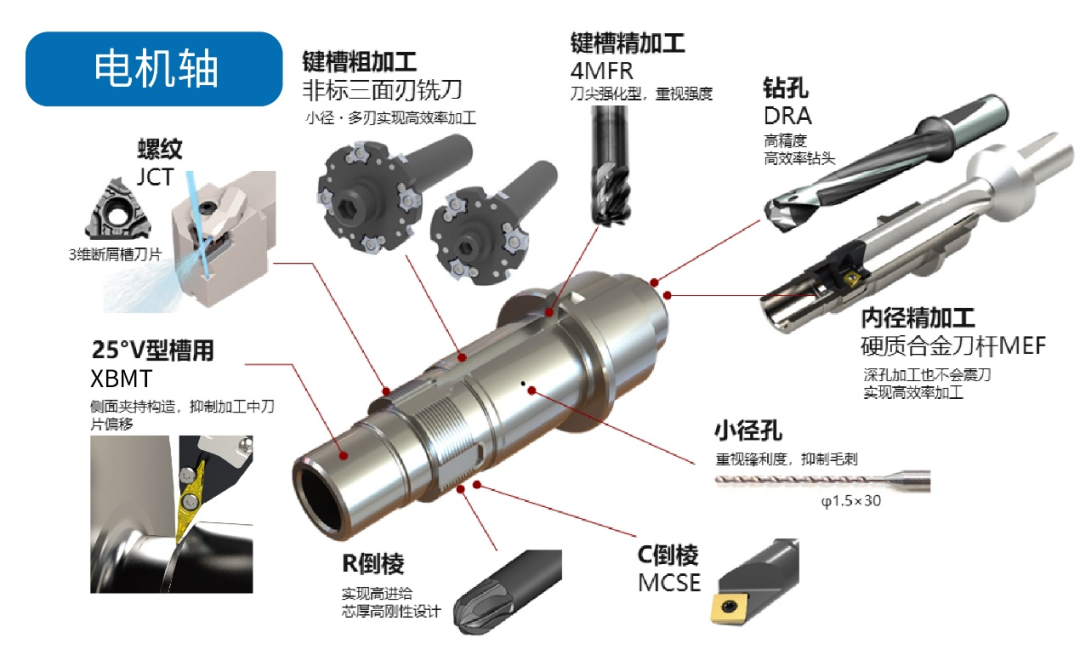
图源:京瓷
磨削加工,在机械加工中隶属于精加工,加工量少、精度高。电机转轴在外圆磨床上进行,用以磨削轴类工件的外圆柱、外圆锥和轴肩端面。磨削时,分为两种:
纵向磨削法:工件低速旋转,如果工件同时作纵向往复移动,并在纵向移动的每次单行程或双行程后砂轮相对工件作横向进给
切入磨削法:如果砂轮宽度大于被磨削表面的长度,则工件在磨削过程中不作纵向移动,而是砂轮相对工件连续进行横向进给。
一般切入磨削法效率高于纵向磨削法。如果将砂轮修整成成形面,切入磨削法可加工成形的外表面。
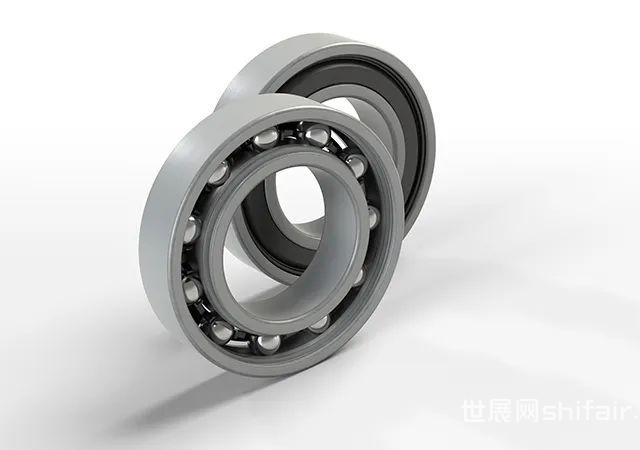
电机高速滚珠轴承 图源:精工株式会社
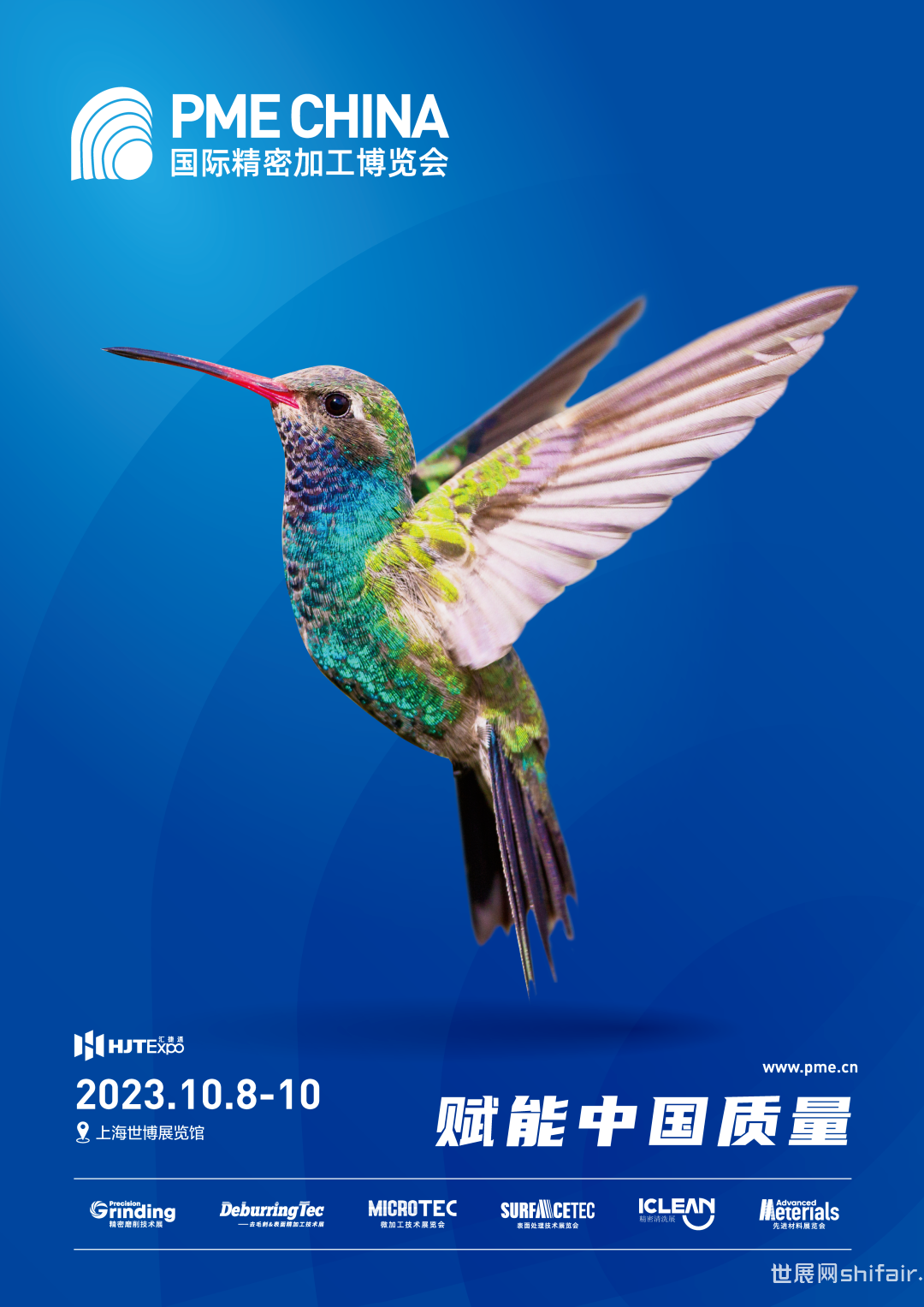