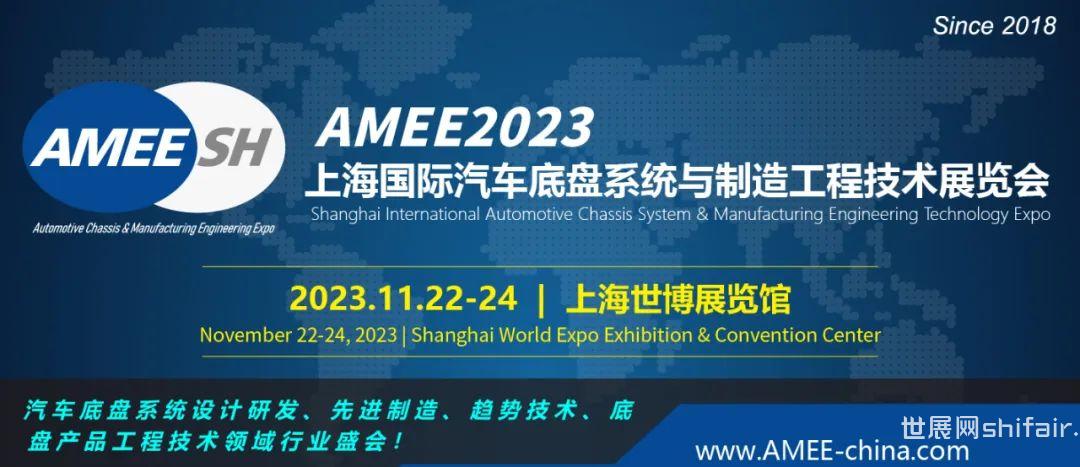
引言汽车副车架是底盘的重要部件之一,支撑前后车桥和悬挂,使用副车架能够提高汽车的舒适性和安全性。现在汽车厂商广泛使用铝合金材料替代钢材料来达到轻量化的目的,通过三维软件建模以及有限元软件进行分析校核可以高效完成副车架的设计工作。然而,铝合金副车架的结构特点决定了其铸造和机加工的难度大幅增加,不合理的加工方法可能会导致气孔、缩松、夹渣以及变形等质量问题。本文首先对原有结构进行了优化设计,并通过有限元分析对其强度、刚度以及模态性能进行了验证。然后根据副车架的铸造和机加工难点,分别设计了铸造工艺和机加工方案,加工完成的副车架没有出现加工问题。最通过台架疲劳耐久试验和耐腐蚀性试验对副车架进行了验证。一、副车架结构优化设计将铝合金材料直接替换铸铁的副车架无法保证其性能要求,所以需要进行优化设计。其优化过程主要经过多轮拓扑优化、CAD设计以及CAE分析等,副车架优化后的结构如图1所示。
图1 副车架优化后的结构针对副车架结构主要有以下几个改动:①副车架底部增加盖板,形成封闭腔结构,增加了刚度与模态性能;②对肋板进行了改进设计,使其满足性能要求。新设计的副车架质量为11.76 kg,相比原来的17 kg,减重比例达到30.8%。二、副车架有限元仿真分析副车架材料采用铝合金ZL114A-T6,其材料参数见表1。将副车架三维模型导入Nastran有限元分析软件中,网格划分的单元类型为CTETRA(二阶四面体)。表1 副车架材料参数
2.1 副车架强度分析选择1 g垂直加载、3.5 g垂直加载、左前轮3 g垂直加载、右后轮3 g垂直加载、左转、右转、刹车、刹车左转以及刹车右转等9种汽车运行工况对副车架进行强度分析,根据工况分别对副车架各硬点位置施加不同的载荷。通过静强度分析,发现在刹车工况下,其强度分析数值相较于其他工况最高,分析结果见表2,分析云图如图2所示。表2 刹车工况强度分析结果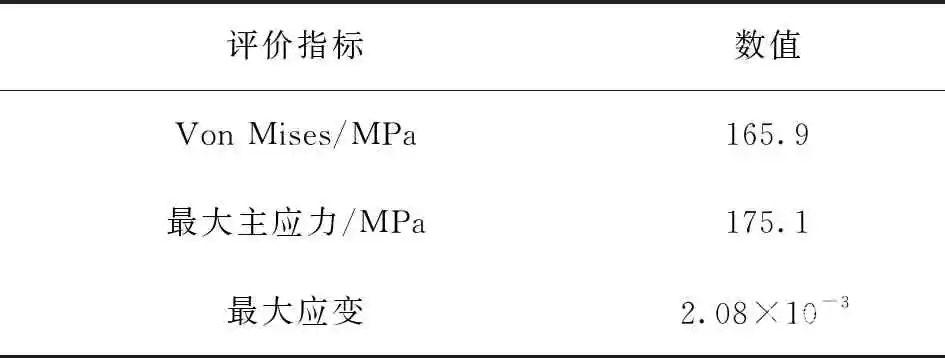
图2 刹车工况强度分析云图由图2和表2分析结果可知,该副车架满足强度设计要求。2.2 副车架刚度分析对副车架有限元模型设定边界条件,其刚度约束如图3所示,通过对其关键部位的硬点刚度进行分析以评价硬点刚度的性能。
图3 副车架刚度约束由图3的有限元分析结果发现,副车架各个安装点的刚度均达到目标要求,其中最大变形发生在下控制臂右后安装点。下控制臂右后安装点刚度分析结果见表3,其X向、Y向、Z向位移云图如图4至图6所示。
图4 下控制臂右后安装点X向位移云图表3 下控制臂右后安装点刚度分析结果
图5 下控制臂右后安装点Y向位移云图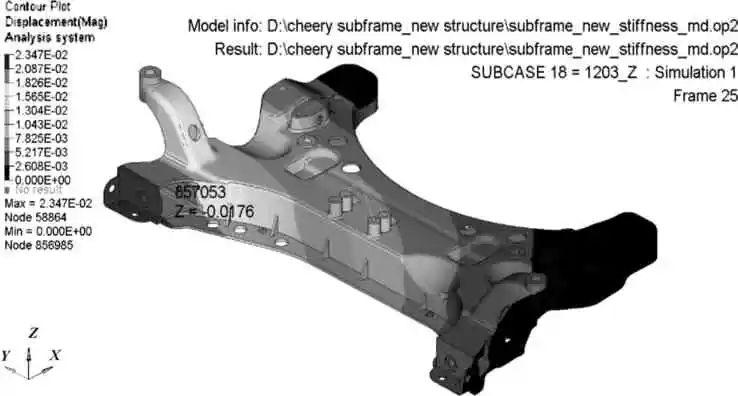
图6 下控制臂右后安装点Z向位移云图2.3 副车架模态分析本文主要考虑了低阶固有频率对副车架的影响,其自由模态和约束模态一阶弯曲振型云图分别如图7和图8所示。
图7 副车架自由模态一阶弯曲振型云图
图8 副车架约束模态一阶弯曲振型云图由以上振型云图可知,自由模态一阶弯曲频率为281.9 Hz,约束模态一阶弯曲频率为372.7 Hz,都大于250 Hz,满足设计要求。三、副车架加工工艺设计3.1 副车架铸造工艺设计针对副车架铝合金铸造工艺,目前国内外流行的主要有高圧铸造、挤压铸造和重力铸造等。高压铸造工艺是通过高压下高速冲型,使得液态铝合金凝固结晶,得到的毛坯表面光洁度好,强度和硬度都比较高,有较好的力学性能,但是延伸率较低,而且无法对其进行热处理;挤压铸造是通过将液态金属倒入敞口模具中,使其形成初步形状再施加高压完成毛坯制作,其力学性能好、尺寸精度高,后期可以进行热处理;重力铸造是在重力的作用下注入铸型,晶体组织不够致密,但可以通过后期热处理来增强力学性能。出于制造成本和数量的综合考虑,本文选择工艺成熟、成本较低的重力铸造方式。
砂型重力铸造的砂型模具目前有传统方法和3D打印两种方式完成。传统的砂型制造流程一般为:CAD设计→工艺仿真→模件制作→工装夹具制作→砂型模具制造→铸造。3D打印的砂型铸造流程为:CAD设计→工艺仿真→砂型模具3D打印→铸造。通过3D打印砂型模具有效简化了传统砂型制造的流程,大大提高了生产效率,因此本文选择3D打印砂型工艺。
由于在铸件的凸台以及厚大部位均有容易产生疏松、缩孔等缺陷的风险存在,而且铸件壁厚较薄,为异型结构,在成型收缩过程及后续热处理时,易发生扭曲,导致大平面变形。本文考虑在前后端面以及厚大位置设置冒口,冒口加快铸件厚大区域的凝固速度,避免产生内部疏松缺陷,并且采用前后多点进胶流道设计,减少进胶时间,减小壁厚较薄处的凝固速度。所设计的铸造模具结构如图9所示,排气口、冒口和浇注流道示意如图10所示。
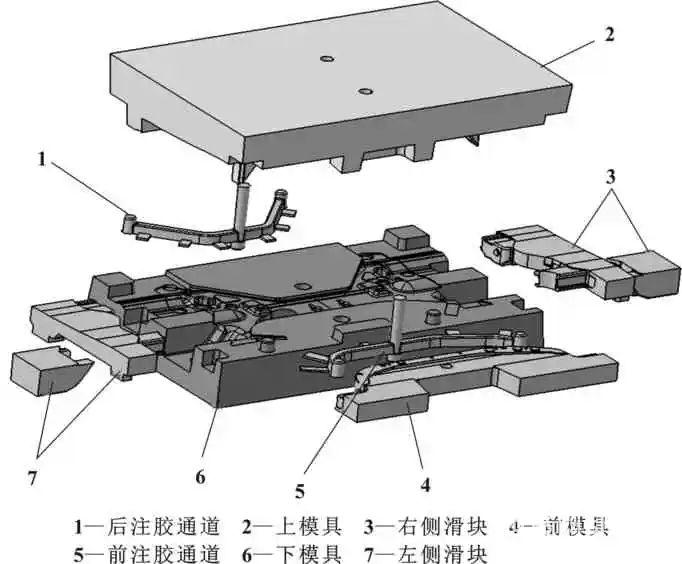
图9 铸造模具结构
图10 排气口、冒口和浇注流道示意
铸造完成的副车架如图11所示。由图可以看出,该副车架没有出现气孔、缩松、夹渣以及变形等铸造问题。
图11 铸造完成的副车架3.2 副车架机加工设计需要对上述铸造完成的副车架进行机加工处理,考虑到副车架的结构特点,机加工主要有以下几个难点:①零件为薄壁筋板类零件,采用砂铸,毛坯不易找正;②零件筋板多、结构复杂、壁薄,为对称结构,壁厚只有5 mm,加工易变形;③零件上下左右前后均有孔系,为对称孔系,且工件尺寸较大、加工要求较高。针对以上难点,设计的整体加工方案分为粗加工留余量后精加工,在加工过程中采用专用工装,配辅助支撑加以装夹。粗加工过程是先以筋板面螺钉搭子、孔搭子作为粗定位基准,对顶面进行粗加工,如图12所示。之后以粗加工顶面定位,对筋板上螺钉搭子、孔搭子及周边加工部位进行粗加工,如图13所示。精加工过程重复上述顺序。经过机加工的副车架尺寸精准,没有出现变形现象。
图12 副车架顶面粗加工
图13 副车架筋板面粗加工四、试验验证4.1 副车架耐久性试验加工完成的副车架应符合奇瑞Q/SQR S5-49规定的要求,为了验证其耐久性,对其进行横向力加载和纵向力加载疲劳寿命试验。试验设备采用MTS汽车零件试验系统专用试验工装,副车架横向力加载和纵向力加载试验分别如图14和图15所示。副车架安装同实车状态,四点固定,等效安装控制臂,加载点为左右控制臂球头处,左右两边同时加载,左右载荷同步、同频、同值。
图14 副车架横向力加载试验
图15 副车架纵向力加载试验表4 副车架耐久性试验条件
经过200 000次的横向力和纵向力加载之后,副车架没有出现裂纹,这说明该副车架耐久性好,满足Q/SQR S5-49 中规定的要求。4.2 副车架耐腐蚀性试验副车架常常处于恶劣的工作环境,所以有必要评估副车架的耐腐蚀性,验证其是否符合Q/SQR S5-49中规定的要求。如图16所示,将副车架置于中性盐雾试验箱中,向其喷射中性盐雾,试验时长为240 h。
图16 副车架耐腐蚀性试验试验完成后,观察到副车架的外观无明显腐蚀,这表明该副车架的耐腐蚀性好,符合Q/SQR S5-49中规定的要求。五、结论本文主要对铝合金副车架的设计开发过程进行了介绍,并通过试验验证了该副车架满足开发要求,具体结论如下:(1)将铝合金作为副车架的材料,对副车架的结构进行了优化设计,并通过Nastran有限元分析软件验证了其强度、刚度和模态性能;(2)对副车架的铸造和机加工方案进行了设计,加工出来的副车架无加工缺陷;(3)对加工出的副车架进行了耐久性和耐腐蚀性试验,试验结果均满足要求。文章来源:《汽车零部件》 希骥车身与附件 车乾信息
AMEE2023上海国际汽车底盘系统与制造工程技术展览会将于2023年11月22-24日在上海世博展览馆举办,预计将有300家全球优秀供应商展示底盘设计与研发、底盘系统轻量化工艺、智能底盘技术(CTC/CTB/CTP技术)、新能源汽车底盘(电池包/电池壳/电驱动)、底盘电动化(线控制动/转向/滑板底盘)、底盘零部件先进制造工艺(冲压/焊接/机加工/装配/铸造/压铸/涂装/总装)、底盘装配与集成技术、底盘零部件检测与测试、底盘车辆工程与动力学、底盘电子与控制技术、底盘系统零部件(制动系统/转向系统/传动系统/悬架系统/副车架)、自动驾驶与底盘趋势等技术解决方案,展会同期举办12个品牌论坛,将邀请近150位来自整车、底盘系统领域的技术专家、教授、供应商代表等嘉宾出席主题演讲,是不可过错的行业盛会。
上海国际汽车底盘系统与制造工程技术展览会(简称:AMEE)创办于2018年,是全球汽车底盘工程技术领域的旗帜展览会,AMEE为中国汽车底盘技术创新与持续发展搭建了高质量平台,为促进全球汽车制造商综合竞争力的提升提供重要支撑,已成为汽车底盘研发、技术、工艺、采购、质量和管理人员每年必参加的重要活动之一。
主办单位:
AEE汽车技术平台
米创博隆展览(上海)有限公司
展会官网:
www.AMEE-china.com
联络我们:
米创博隆展览(上海)有限公司
Micreative-Bolong Exhibition (Shanghai ) Co.,Ltd
项目一部:
电话:021-64081106、64081107
邮箱:info1@amee-china.com
项目二部:
电话:021-54700961、54701073
邮箱:info2@amee-china.com
AMEE2023展位预订咨询:
Jeff Shen:185 2135 8883
alin Xie :159 2166 5818
Allen Shen:183 2121 1115
Kevin Li:176 2147 8850
Lina Wang:182 2134 7866
Cindy Gu:178 5637 9116
Anna Lv:175 2118 5532
AMEE2023展位及同期会议预订点击 “阅读全文”